Revolutionizing Aviation: The Impact of Aerospace Composites
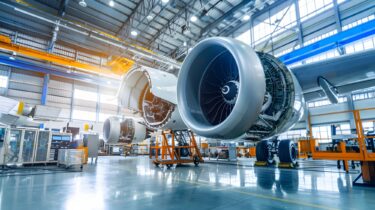
The aviation industry is constantly evolving. Innovative technologies are allowing aircraft to become lighter, stronger, and more fuel-efficient while also enhancing performance and capabilities. One innovation that has greatly impacted aviation is the development of advanced composite materials for aerospace applications. These materials are revolutionizing aircraft design.
What Are Aerospace Composites?
Aerospace composites are made by combining two or more component materials with different physical and chemical properties to create a new material with enhanced strengths and advantages over either individual component. According to the experts at Aerodine Composites, they typically comprise strong load-bearing reinforcement fibers, like carbon fiber or fiberglass, embedded within and bound by a plastic polymer resin matrix into a lightweight yet durable composite material.
Compared to traditional aluminum aircraft builds, composites can deliver higher strength-to-weight ratios and excellent corrosion and fatigue resistance properties while allowing more aerodynamic and optimized part fabrication. The resin matrix protects and supports the reinforcement fibers and gives the composite its shape, while the fibers strengthen the matrix by imparting their physical and mechanical characteristics.
Benefits of Aerospace Composites
There are several key benefits that aerospace composite materials offer over traditional metal builds:
- Lightweight – Composites can weigh up to 50% less than metals. This greatly affects fuel efficiency and performance by enabling larger payloads.
- High Strength – Composites can match or exceed the specific strength of comparable metal parts, even at high temperatures. This allows lighter builds without sacrificing structural integrity.
- Corrosion Resistance – Composites do not corrode like metals which degrade over time. This reduces maintenance costs over the aircraft’s service life.
- Fatigue Resistance – Composites have high fatigue and crack growth resistance compared to metals. This improves safety and longevity over thousands of flight cycles.
- Design Flexibility – Complex and optimized shapes can be molded as a single aerodynamic part, avoiding multiple component assemblies. This supports superior aerodynamic designs.
- Electric Properties – Carbon composites allow for lighter and less expensive grounding and shielding compared to metal aircraft. This enables more cost-effective electrical systems integration.
- Thermal Insulation – Composites provide outstanding thermal insulation compared to metals, helping regulate cabin temperatures and better retain heat in engine components.
- Vibration Dampening – Composites have excellent vibration absorption properties, resulting in lower noise levels in the aircraft cabin.
Applications in Modern Aircraft
The unique properties of aerospace composites have seen their penetration across nearly all new aircraft builds over the past decades, including both civil and military programs. Some examples include:
- Airframe – The Boeing 787 airframe is over 50% composite by weight, from wings, tail sections and fuselage barrels to doors and flight control surfaces. Composites translate into 8% better fuel economy.
- Engines – Modern turbofan engine designs use composites extensively in fan blades, nacelles, cowlings, exhaust systems, casings, and other components. This allows larger fans and higher bypass ratios for better fuel efficiency.
- Interiors – Modern aircraft cabins contain composites in galleys, lavatories, partitions, ducts, ceiling and sidewall panels, floors, and baggage bins. Lighter interiors increase payload capacity.
- Avionics – Radar domes and antenna housings use composites for their transparency to electromagnetic signals and lighter weight installations.
Conclusion
The development of advanced composite materials purpose-built for aviation is truly revolutionizing aircraft design. Their lightweight yet stronger builds, corrosion and fatigue resistance requiring less maintenance and excellent thermal and acoustic insulation properties are delivering remarkable improvements in efficiency, economics, and capabilities.
Aerospace composites have solidified their permanent role as a core building block in modern aviation. Their high strength-to-weight ratios, design flexibility and durability will be crucial for next generation aircraft innovations ranging from state-of-the-art airliners to innovative military programs and space exploration vehicles pushing technology ever further.